Процесс производства пластиковых труб
Пластиковые трубы применяются повсеместно: на рудниках и в шахтах, ГОКах и ТЭЦ, в химической и пищевой промышленностях, в быту. Процесс производства пластиковых труб очень прост и полностью автоматизирован, а также не требует специальных материалов и больших трудозатрат.
Оборудование для производства труб из пластика
Постоянный рост производства обусловлен все большей востребованностью пластиковых труб в связи с их ценными эксплуатационными качествами:
- они невосприимчивы к коррозии, обладают высокой химической стойкостью и способностью выдерживать агрессивные среды;
- трубы обладают долгим сроком службы;
- не нужна катодная защита;
- не отлаживаются жировые накопления, поэтому диаметр трубы не сужается;
- с применением пластиковых труб снижаются теплопотери из-за низкой теплопроводности;
- вероятность разрушения трубы из пластика при замерзании внутри жидкости ниже, чем у аналогов из металла;
- малый вес изделий делает монтаж менее трудоемким.
Сырьем для производства пластиковых труб могут служить полибутилен, поливинилхлорид, полипропилен, полимерные материалы и даже вторсырье – пластиковые бутылки или пленочные отходы, одноразовая посуда, корпуса от техники и аппаратуры и прочий мусор.
Оборудование достаточно простое и немногочисленное. Основа всего производства – экструдер. Это специальный станок для изготовления пластиковых труб. Весь процесс работы станка заключается в выдавливании (экструзии) трубы из горячего пластикового гранулята. Экструдеры бывают:
- Шнековые. Принцип действия метода подобен мясорубке и наиболее распространен.
- Безшнековые с диском.
- Комбинированные одновременно с диском и шнеком.
Производственная линия имеет непрерывный закрытый цикл. В бункер экструдера засыпается полимерный гранулят, где они плавятся с использованием кольцевых нагревателей. Шнек создает вращательное движение, благодаря чему расплавленный пластик переходит в экструзионную голову и там под высоким давлением формируется будущая труба. Станок имеет зону вакуумной калибровки, где происходит формирование диаметра и толщины стенок, а также первичное охлаждение изделия.
Постепенно труба проходит в другую охлаждающую камеру до тех пор, пока полностью не остынет. Продвижение трубы обеспечивается специальным тянущим устройством с гусеницами. За тянущим устройством располагается отрезное устройство, которое формирует отрезки заданной длины. По желанию заказчика трубы могут быть смотаны в бухты или поставляться мерными отрезками. Все производство отслеживается и согласовывается логическим контроллером, которое следит за бесперебойностью и качеством производства.
Как осуществляется контроль за качеством, транспортировка и хранение
Готовая труба должна быть проверена на соответствие следующим параметрам:
- внешний диаметр;
- толщина стенок;
- длина мерных отрезков;
- овальность.
Контроль осуществляется в лабораториях путем проверки отобранных контрольных образцов из произведенной партии. Если продукция соответствует всем нормативным показателям, то лаборант выдаст документ о соответствии качеству. После этого продукция поступает на прилавки магазинов или поставляется заказчику.
Хранится готовая продукция должна в вертикальном положении вдали от нагревательных приборов и скрытая от попадания солнечных лучей. Транспортировать пластиковые трубы можно любым транспортом, но в крытом кузове. Бухты или мерные отрезки должны быть упакованы, а концы труб защищают заглушками от попадания мусора.
Простота технологического процесса производства пластиковых труб, дешевизна сырья, низкая трудоемкость позволяют людям, даже не имеющим большого стартового капитала, открыть свой прибыльный бизнес.
Похожие записи

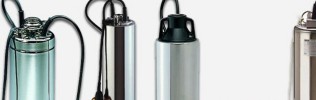
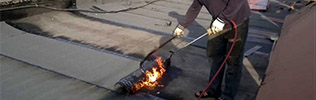
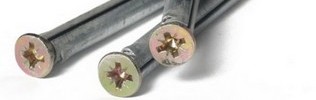
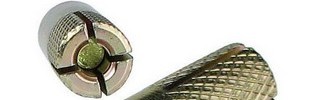
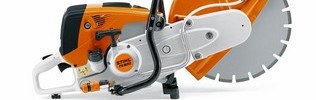
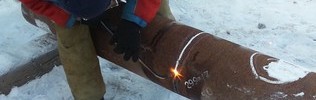
